Defence Production
Benefits of Plastic over Metal
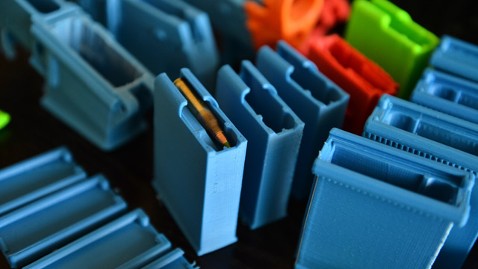
Plastics magazines for guns
Substituting injection molded plastic components for their metal counterparts provides three key
advantages:
1. Lower weight: Plastics are, on average, 40% lighter than metals.
Reducing per-soldier equipment loads allows service members to remain lithe, agile — and, above all, safe — when engaged in maneuvers or combat.
2. Freedom of design and assembly: Injection molded plastic components are subject to fewer assembly constraints,
as manufacturers can consolidate multiple elements into a single plastic part.
The ability to design plastic parts with complex geometries also means multiple parts can be assembled using the method best-suited to a particular application — such as welding, heat staking or mechanical snap-fit.
3. Lower Total Cost of Ownership (TCO): Injection molded plastic parts do not require extensive secondary operations, like machining or painting.
Practicality of injection molded plastic components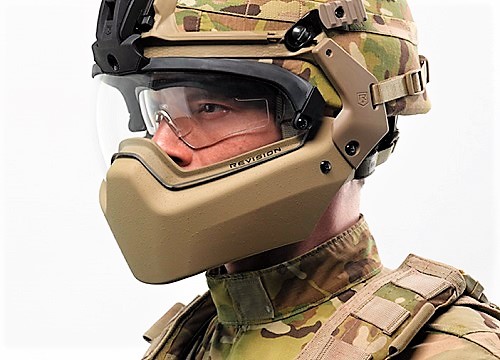
Plus, plastic injection mold tooling is extremely robust and has a much longer life than the die-cast molds used to produce metal parts — a substantial cost savings.
Evaluating these general benefits against specific requirements critical to military/defense applications further demonstrates the practicality of injection molded plastic components:
PORTABILITY
Smaller, lighter devices make it easier for military and public safety personnel to transport, store, access and use equipment under routine and challenging conditions.
Overmolding of soft-touch grips also make operation less
complicated for gloved hands and offer better grasp control in dirty, smoky, oily or otherwise compromised environments.
DURABILITY
There are unique factors in the field to which devices and equipment are exposed and must endure: concussive events, extreme temperatures, frequent drops, dirt, excessive moisture, fires and hazardous chemicals.
Unlike metal that will corrode, dent and potentially malfunction, injection molded plastic components are specifically designed to survive impact, shock and vibration while simultaneously withstanding corrosive environments.
This becomes even more important when equipment like GPS units, other in-field communication technologies or soldiersaving medical equipment contain electronics that must be protected by a plastic housing.
ELECTRONIC DETECTION

Military Jerrycans made of Plastic
Many military operations require personnel and equipment to remain undetected from the opposition.
Metal-based machinery leaves large electromagnetic radar/sonar echo signatures and infrared heat source footprints.
A variety of non-conducting and insulating resins have been introduced to increase the stealth capabilities for military/defense applications:
• Domes constructed from polymer matrix composites shield detection equipment and deaden position-revealing vibration on military ships and aircraft
• Military helicopters outfitted with multi-spectral stealth capabilities (radar, infrared and acoustic) like polymer foam blades and Kevlar-carbon fiber structural materials
• Flexible, polymer matrix-based coatings used on a number of military vehicles to thwart “normal” and “thermal” visual detection
Identification of right Engineering Grade Polymers

Reinforced Plastic Helmets
Between base polymers, additives, and fillers, there are literally tens of thousands of engineering-grade resin options available.
Selecting the right one for your military/defense application can feel like trying to find a needle in a haystack — especially when you factor in potentially competing priorities of mechanical and molding properties with cost and unique, mission critical safety needs.
To identify the right Engineered Thermoplastics and compounds followings issues are important
• The relationship between plastics characteristics and performance for injection molded components
• Which plastics align well with military/defense applications
• How an experienced, complex injection molder contributes to the design and manufacture of safe, reliable and tough plastic components.
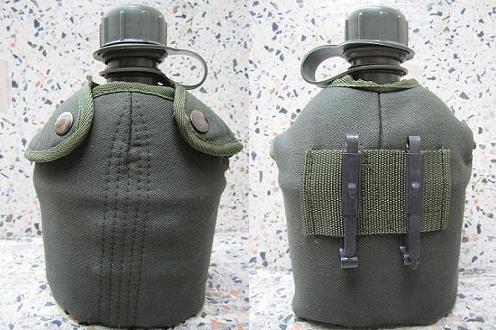
Water Bottles for Combats
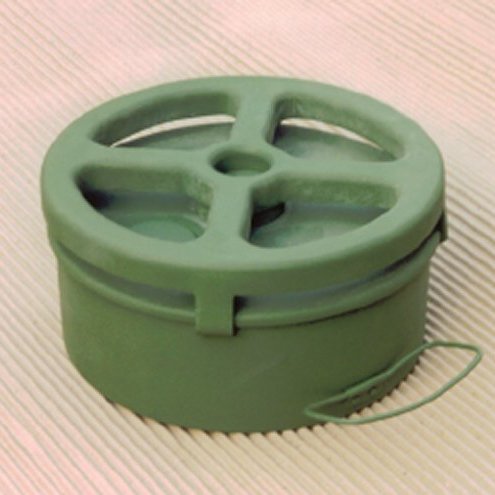
Plastic Shell of Anti Tank Mines